Why I designed and remixed the masks and shields the way I did
- Matt Thomas
- Sep 10, 2021
- 5 min read
Updated: May 17, 2023
When it comes to engineering design, you must follow specifics in order to produce a safe and effective product. Things such as Vonmesis stresses, safety of factor and many many other principles come into play. Now, the above is for machine design and mechanical objects, however, some of those principles are used in medical devices. You dont want a plastic device failing under normal or above normal conditions. When it comes to masks and face shields, there are VERY specific design principles that must be followed. If you want to watch me model the mask in Sketchup, click on the Videos and STLs tab to watch the videos:)
For masks: I will not go into all the details here but I will say this, there is a BIG reason why the defacto for all medical PPE, gloves, gowns, masks etc, is to be able to filter 0.3 microns in size. Now a micron is one thousandth, of a mm.. 0.001mm in size. The reason for this number is no accident. It was not just randomly picked. Turns out that particles at that size of 0.3 microns, float through the air in a very linear path and are the HARDEST to capture. Imagine throwing a baseball through a soccer net. To counter act this linear motion, the mask material is actually statically charged to act as a magnet, so as the baseball passes through the net, the static charge grabs onto it and pulls it to the net. Here is where things get really interesting, turns out that particles smaller than 0.3 microns, are small enough to bounce off of gas particles in the atmosphere such as o2, nitrogen etc, making them far easier to catch, than 0.3 microns. Brownian motion is the fluid dynamics principle behind this. I have studied Brownian motion and fluids extensively. This is like bouncing a baseball into a soccer net, more of a chance to not pass through. This is why the idea of viruses being able to pass through masks is false thinking, also, viruses do not work that way either. We do not breath out viruses, i repeat, we do not breath out viruses. In order for a virus to infect humans, they have to take over a living cell in order to use the living cells organs, energy and food supply to replicate more viruses since a virus is non-living. These host cells are actually what we breath out, which we call respiratory droplets. these droplets are very large in size compared to viruses, they are actually 0.4 to 1 microns in size and are to heavy and large to pass through mask material. A standard 600 Thread Per Inch (TPI) single layer cotton will filter out 97% of 0.4 micron sized particles. The smallest size of host cell capable of allowing virus replication is about 0.4 microns in size. Now lets say, some of the virus particles somehow leave the host cell, again, we actually have two deterrents for that. First, the plastic material used in masks is made from electrostatically charged spun polypropylene which acts as a magnet, attracting the smaller particles to stick to it, second, Brownian motion due to the smaller particles bouncing around.
Ok, knowing this information now, what i did was designed a 3D printable mask that followed these guide lines as well as the specifications for a face mask outlined by medical engineers such as myself.
Must cover mouth and nose
Must fit firmly around surfaces and contours
Needs to minimize the amount of airflow between skin and mask
Made from non-toxic materials, as well as non-latex
No vents or valves that allow non filtered O2 to pass
Comfortable for long periods of time and breathable
Either multi-layer cloth or solid thermoplastic for the body of the mask
High quality filter material, 600TPI cotton, or polypropylene
Most of these specifications are common sense, but some are not. You would be surprised at how many face shields and masks were sent to hospitals, that used standard rubber bands and elastic as the attachment method. This is an issue because some people have a latex allergy and could you imagine dealing with a sudden allergy right in the middle of this mess?
There are more specifications needed for a N95 mask, however, those are for the material of the mask itself. IE, electrostatically charged spun polypropylene for the filter, ultrasonic welded for any type of bonding, and then a non-absorbent outside material. Also remember that Doctors and healthcare workers can NOT social distance themselves from their patients, so they require a higher-grade mask than what the general public will ever need, unless you ride on a subway, a bus, a rail car, or other places where social distancing is almost impossible. This is why I made sure to use ONLY electrostatically charged spun polypropylene from 3M furnace filters because it is the "higher-grade" and can be used in tight quarters or any other situation:) When you pick out the filter material, use 1500 advanced allergen or above:) BUT, not everyone can get their hands on this material. Here at my local Walmart, they have TONS of it!! If you find yourself in a bind, use a single layer of 600 Thread Per Inch cotton as the filter material. This will provide 96% filtration of 0.4 microns and higher sized particles, and try to keep some distance:)
Each 3M filter is a 20x20x1 inch box with the filter material in it. The material has been folded in such a way that it UN-folds to roughly 10 feet in length. Each filter frame can make well over a thousand filters. Each filter can last up to a week, especially if you sanitize it in the oven by baking it at 170-to-200-degree F for 20 minutes. DO NOT USE WATER OR LIQUID. It will ruin the static charge, making them useless. Either bake, or simply replace. You can wash the mask body in warm soapy water and it will sanitize the parts just fine. I did my thesis on this concept. Please refer to the article "Is It Food Safe?"
Speaking of the body of the mask, let's talk about how it SHOULD be printed. There is A LOT of talk about using SLR nylon printing over FDM and PLA for making masks. This is actually a bad idea. The number one reason NOT to use SLR or SLS printing with nylon powder, is simply because SLR prints are 30% MORE porous than regular FDM prints.
"A typical SLS printed part is about 30% porous. Porosity gives SLS parts their characteristic grainy surface finish. It also means that SLS parts can absorb water, so they can be easily dyed in a hot bath to a large range of colors but also that they require special post-processing if they are to be used in a humid environment."
As you can read, they have more irregularities in them than FDM. Again, please refer to my food safe article about how solid PLA fdm prints really are. A 2 walled print held water for over 24 hours, a 3 walled print held water for over 7 days before I tossed it out. This is exactly why I chose to use basic PLA FDM printing. It simply works!!
I have three mask designs, one with a grill grate pattern on the front, which acts as a splash shield, one without the grill in the front, and finally, the mask with a very LARGE breathing space. It's up to you which one you like the best:)
For the Face Shields:
Face shields are a lot simpler in their design than masks. You want to make sure that the brim is NOT hollow. Alot of volunteers with 3D printers tried to find the easiest shields to print, while saving time and material. What ended up happening is a hollow brim above the forehead. This defeats the purpose of the face shield since it allows particles to fall into the respiratory path, then we breath them in, if not wearing a mask. Ideally you should have a mask on under a shield. The plastic face protector should cover from ear to ear, from forehead to chin.

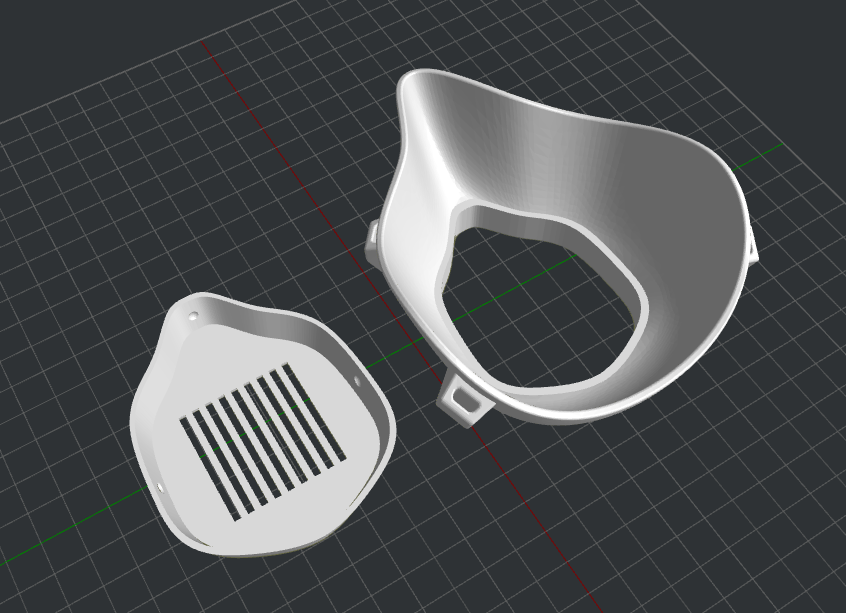
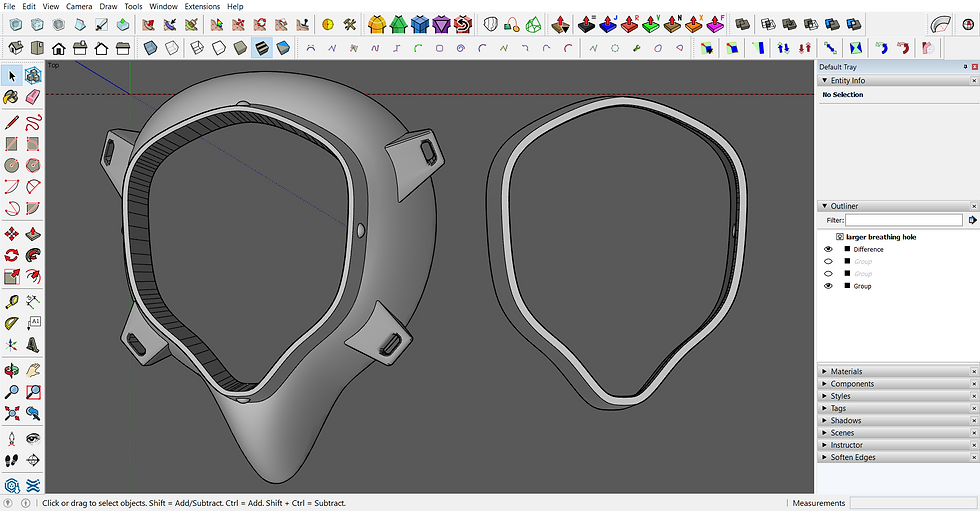